The Golden Rules of Injection Molding Part Design: Get It Right From the Start
When it comes to designing plastic parts for injection molding, the decisions you make upfront can make or break your timeline, tooling cost, and part quality. At Onit MFG, we specialize in working with engineers early in the development cycle to reduce design risk, shorten lead times, and hit production goals with confidence.
Here’s a breakdown of key injection molding design principles we live by—and why they matter when you’re designing parts that need to perform in the real world.
1. Uniform Wall Thickness = Predictable Parts
The #1 design rule in injection molding? Keep wall thickness consistent.
When wall thickness varies too much across a part, it creates problems like sink marks, voids, warping, and uneven cooling—all of which can impact strength, cosmetics, and dimensional stability.
Best Practice:
Maintain consistent wall thickness throughout your part whenever possible. If thickness transitions are necessary, use gradual tapers or fillets to smooth the change and prevent stress concentrations.
Onit Tip:
Material-specific wall thickness matters too. For example, 1.5–3.0 mm is a typical sweet spot for many commodity resins. We’ll help you dial in what’s ideal for your application.
2. Draft Angles Make or Break Tooling
Draft is the slight taper applied to vertical surfaces to help parts eject cleanly from the mold. Without proper draft, you risk part sticking, scuffing, or worse—tool damage.
Best Practice:
Apply 1° to 2° of draft per side for most surfaces. Increase it on textured surfaces or deep cores. The deeper the draw, the more draft you need.
Onit Tip:
Draft isn’t just about manufacturing ease—it protects your part surface, reduces cycle time, and extends mold life. We review and optimize draft angles on every part we run.
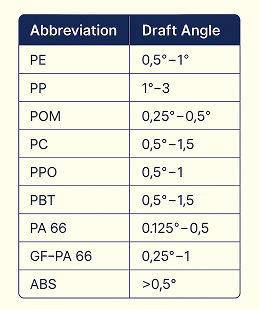
3. Radii Prevent Stress—and Tooling Heartache
Sharp corners are a red flag in injection molding. They create stress risers in parts and stress points in tooling. Adding generous radii (internal and external) improves part strength and tooling durability.
Best Practice:
Use inside radii at least 0.5× the wall thickness and match external radii for uniform flow. Avoid 90° internal corners wherever possible.
Onit Tip:
Fillets aren't just cosmetic. They promote material flow and reduce pressure spikes during molding, which directly impacts cycle time and surface finish.
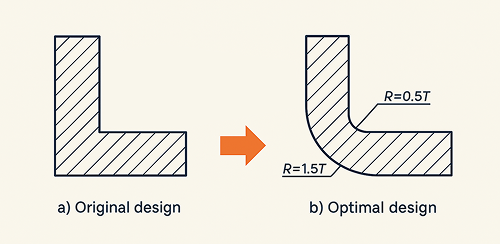
"The Onit team truly is an extension of our Manufacturing group. I've never had more confidence going into Production Injection Molding."
4. Ribs & Bosses: Reinforce Without Overbuilding
Ribs and bosses add strength without adding mass—but only when designed correctly.
Best Practice for Ribs:
- Max thickness = 60% of wall to avoid sink
- Height ≤ 3× wall thickness
- Include draft (0.5°–1°)
Best Practice for Bosses:
- Wall thickness = 60–80% of nominal wall
- Add radii where boss meets base
- Connect with ribs when possible
Onit Tip:
We see a lot of overbuilt bosses and ribs that lead to sink marks or filling issues. Our DFM process balances structure with manufacturability.
5. Avoid Undercuts (Unless They're Worth It)
Undercuts add complexity—and cost—to mold tooling. If your part traps the mold in any direction, it requires side actions or lifters to release it.
Best Practice:
Design for straight pull molds whenever possible. If undercuts are needed (snap fits, threads, holes), weigh the cost/benefit of lifters or collapsible cores.
Onit Tip:
Sometimes an undercut is the right answer—but we’ll flag when it’s driving unnecessary cost or slowing lead time. We’ve solved complex undercut challenges with modular tools and creative parting lines.
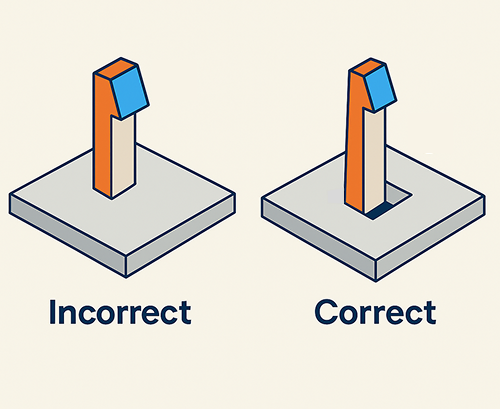
6. Gate and Ejector Locations Matter
Part design isn’t complete until we know where the resin will flow—and where the part will eject.
Best Practice:
Design parts with gate and ejector pin placement in mind. Avoid cosmetic areas and reinforce ejector zones. Be ready to tweak geometry to support better gating.
Onit Tip:
We often work backward from mold flow simulations to recommend subtle design shifts that dramatically improve fill, venting, and cooling.
Partner Early. Iterate Fast. Manufacture Smarter.
At Onit MFG, we help product teams move from prototype to production without tripping over preventable design issues. Our engineers review every part for injection molding best practices and offer real-time feedback on DFM, material choices, and cost-saving opportunities.
Looking to get a second set of eyes on your injection molded design?
Let’s walk through it together. We’re here to get you to great parts—faster, cheaper, and with fewer surprises.
Don’t wait pal, start moving the needle in your business today with our broad-ranging solutions built around your specific business needs.
Get Started