For many product teams, the jump into injection molding feels like a point of no return. The upfront cost of tooling, combined with the fear of locking in a design that’s not quite final, can stall decision-making—and ultimately delay getting real parts in real materials.
At Onit MFG, we see this hesitation all the time. And we get it: no one wants to invest in tooling only to realize a key feature needs adjusting. But here’s the good news—modern injection molding isn’t as rigid as it used to be. With today's supply chain advancements and better access to rapid tooling partners, it's never been faster, more affordable, or more flexible to get into molded parts.
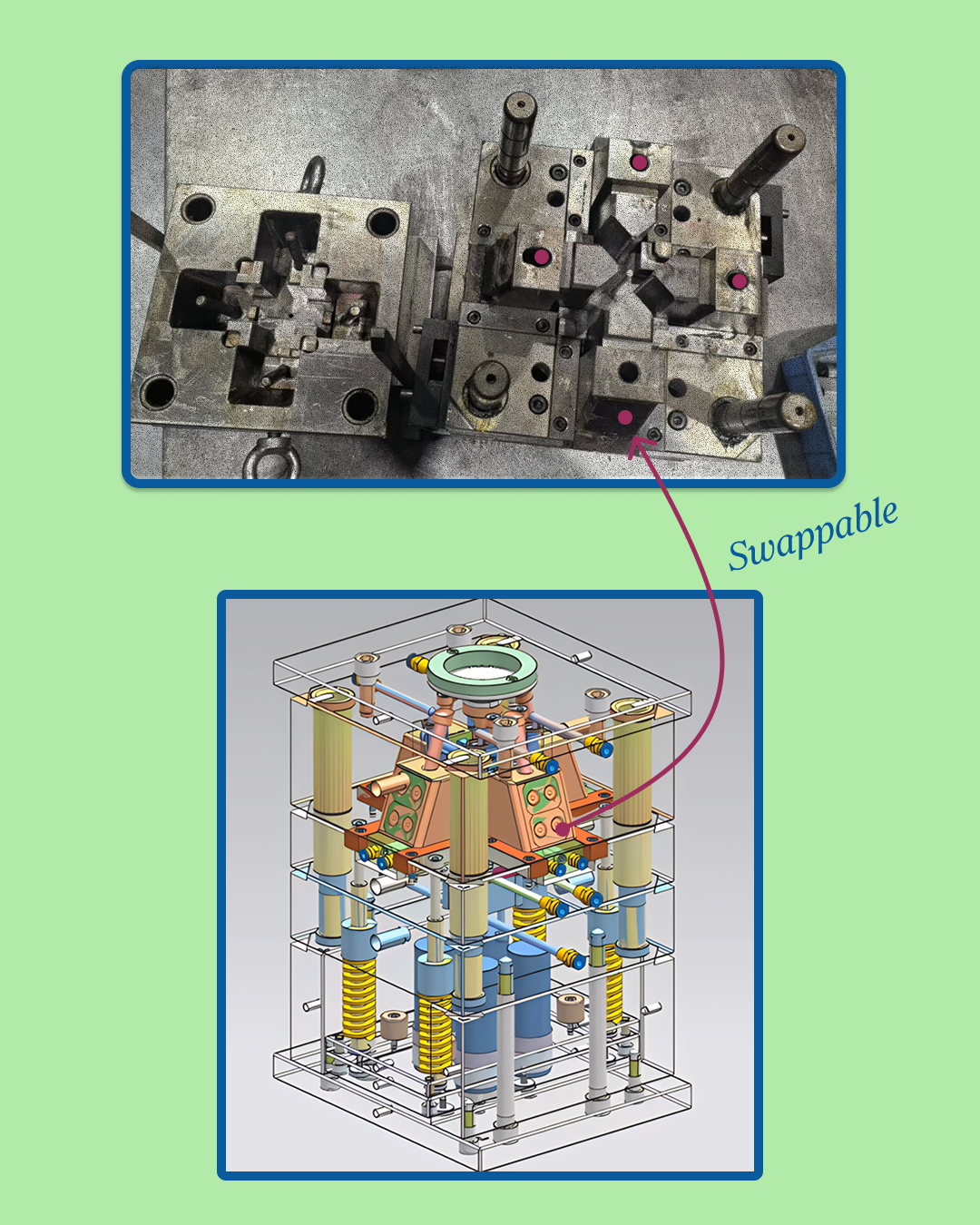
One of the most overlooked strategies for design flexibility is modular tooling, also known as tooling with swappable inserts. These inserts allow us to isolate specific features of a part—like a clip, a port, or a logo—that might change during the development process. Instead of reworking the entire mold, we simply swap out that section with a new insert.
"Onit Mfg has delivered cost-effective, high-quality molds, mold bases and cavities on time and to specification. The craftsmanship and accuracy of the mold-tooling have noticeably improved the quality of Lemo products by increasing yields and reducing cosmetic errors and waste by over 20%."
Here’s why that matters:
- Faster modifications – Smaller inserts are quicker to machine than full mold halves.
- Lower cost – You only pay for the area being changed, not an entirely new tool.
- Iterate with confidence – You don’t have to freeze your design completely before tooling.
- Scalable to production – Modular inserts aren’t just for prototyping; they’re used in production-class tools to support product variations without starting from scratch.
This tooling approach is especially helpful when you know a feature might evolve. Let’s say there’s a functional area that might be removed or redesigned later—we can build the tool around that assumption and design in a modular insert for that section. That way, your team can start molding production-grade parts now, without waiting on final approval for every last feature.
The result? You move faster. You gather feedback sooner. You reduce risk.
Bottom line: If getting into your end-use material early is valuable to your project (and it usually is), don’t wait. Our team can help you design a smart, modular tooling approach that keeps iteration easy and costs low—so you can move forward with confidence.
Don’t wait pal, start moving the needle in your business today with our broad-ranging solutions built around your specific business needs.
Get Started