What is a Bump-Off in Injection Molding?
A bump-off is a type of undercut—an intentional design feature that temporarily interferes with the mold’s opening direction. It’s used when a part needs to flex slightly to release from the mold without requiring complex side-actions or cams.
Think of the snap on your jacket. With just the right force, it pops into place and releases cleanly. That same mechanical principle is at play in plastic components like twist-off caps, closures, and fit-to-lock features molded into polypropylene (PP) or HDPE parts.
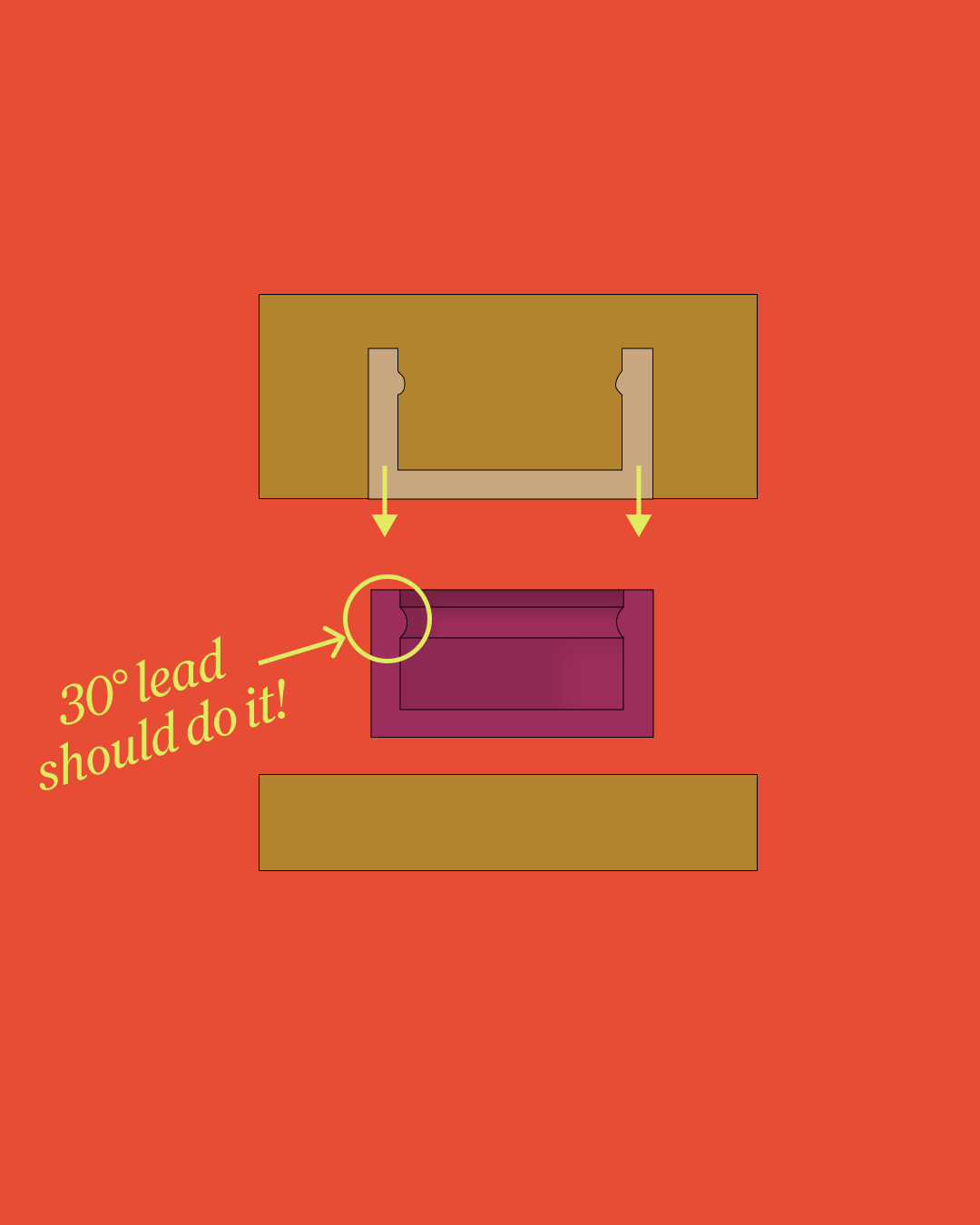
Why Bump-Offs Matter in Part Design
Materials like polypropylene (PP) and high-density polyethylene (HDPE) are flexible enough to deform slightly during ejection and return to their original shape. That’s why these plastics are great candidates for bump-off features—they avoid the need for extra tool actions like unscrewing cores or side cams.
The payoff?
- Simplified tooling
- Faster cycle times
- Lower production costs
A well-placed bump-off can be the difference between over-engineering a mold and getting clean, repeatable parts at a fraction of the cost.
"Whenever I am in a pinch, Onit is the first team reach out because they know how to get the job done right."
Optimize Your Part Design for the Real World
At Onit MFG, we help customers take advantage of design strategies like bump-offs early in the process—so you don’t get stuck with avoidable costs or production delays later.
We’re here to guide you through the nuances of injection mold part design, material selection, and manufacturability—especially the stuff you didn’t know to ask about.
Need help with your next part design?
Reach out to the Onit crew and let’s simplify the complex—together.
Don’t wait pal, start moving the needle in your business today with our broad-ranging solutions built around your specific business needs.
Get Started