Finishes / Color match / Assembly / Tolerances
Finishes Options: When it’s time for production parts, we can match specific mold textures or polish finishes to fit your needs. Plus, we offer performance-enhancing coatings like EMI shielding, soft-touch paint, or clear coat to ensure your parts meet every functional and aesthetic requirement.
Color Match: Urethane casting has a distinct advantage over other prototyping processes: we can cast parts in your custom Pantone color, and to ensure spot-on color matching, we apply a final coat of paint. This means your parts are ready for real-world handling and application—if they get scratched, there won’t be any telltale marks showing the natural resin color underneath. They’re built to withstand the wear and tear while keeping your brand colors intact.
Assembly: These parts are primed for secondary processes just like their production counter parts. Press fit inserts, pad printing, PCB assembly, split and glue – no problem. Since the parts are made from thermosets there are different considerations, but we can likely take care of all of that for you.
Tolerances: Our starting tolerance for urethane casting is typically around xxx/in, which is slightly looser than production part tolerances. This flexibility is ideal for refining the tolerances you’ll need before committing to production tooling. By pinpointing the right tolerances for multi-component assemblies during the urethane casting stage, you can prevent over-engineering and make smart, cost-effective decisions before investing in hard tooling.
Thermoset resins vs Thermoplastic resins?
Alright, let's dive into resins! This section is extra credit for those who want to understand the deeper workings of production methods and their materials.
Urethane Casting vs Injection Molding
Urethane casting often serves as a steppingstone toward high-volume production. Injection molding resins have some key differences when it comes to the raw material chemistry used.
Injection Molding involves melting pellets of the chosen resin and injecting them at high pressure into a metal mold/tool. Once the resin cools, the part is ready to be removed. The resins used here are thermoplastics—they are "one-part" resins that can melt, solidify, and be remelted multiple times. Chocolate, everyone’s favorite treat, acts in a similar way to thermoplastics.
Urethane Casting on the other hand is a bit different. It uses a 2-part mixture of resin and catalyst. This mixture is combined in small batches and poured into a soft mold at low pressure. No added heat is needed, and once cured, these parts are “set” permanently—they can't be melted down or separated again.
SO WHY USE BOTH?
These differences mean that actual injection molding resins can't be used in urethane casting, and vice versa. However, urethane casting is often chosen because its molds are faster and easier to make, providing flexibility and speed for prototyping and short-run production.
To meet these needs, our resin suppliers have developed a robust selection of resins that mimic the qualities of production injection molding resins, so whether you're making prototypes, show models, or end-use parts, urethane casting can offer valuable solutions for product companies.
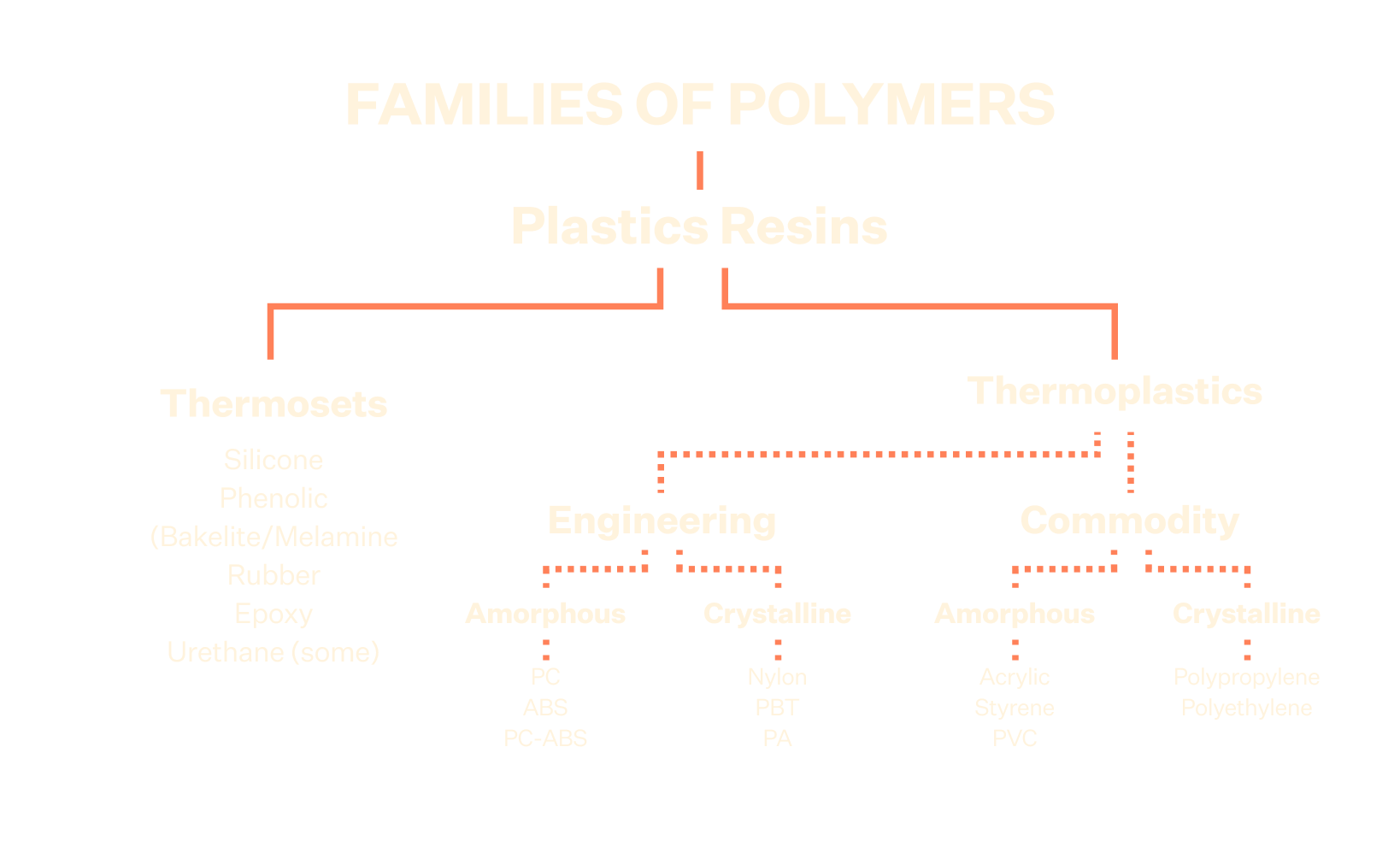
Think Urethane Casting might be the answer ? Check out our no strings attached calculator tool “Instant Calculator"
Get Started